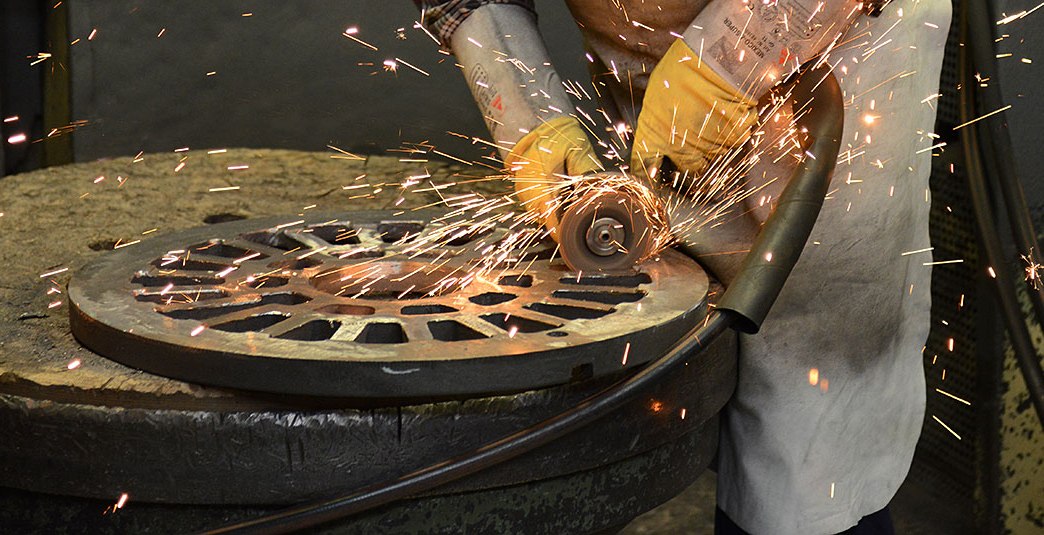
Cleaning Process
The castings are given the finishing touches in our own blow room and, if required, a protection primer according to specifications.Our blowroom is characterized by a high degree of mechanization and by workplaces designed according to the latest ergonomic findings, as well as by flexible blasting options with large parts and through belt blasting systems.